Imaging that we are calling CSV file as Real-Time Sequence on Stimulus Profile. For large size of model file, sometimes the identical data channel of CSV wants to be mapped to the multiple channels.
Of course, we can workaround this issue when we create the multiple channels with the same data on CSV file. However, that would be nightmare if the data size is huge (long-time data).
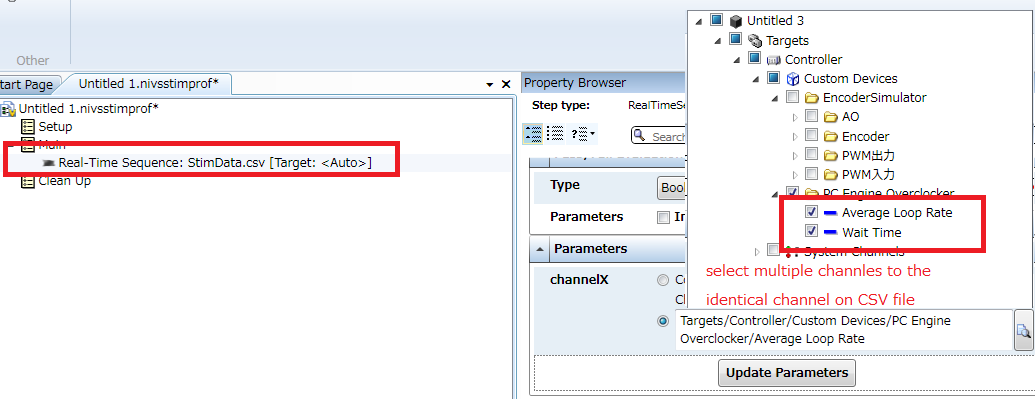