Possibly the assumption here is that you are not using any signal conditioning to make the output from the straing gauge better match the input range available on the USB 6009 DAQ. If your on an educational project this is probably the focus of the project anyway. If your in industry it will be less time consuming to buy in the right conditioning equipment unless the application is very specific and or specialist.
Essentially the 14 bits only limits the dynamic range (the range from minimum to the maximum seen on one scale). Thus with a correctly configured pre-conditioning amplifier, it will work just fine. That is, to make the output microvolts from the strain gauge become more like volts for the A/D convertor input. Correctly configured with scaling you will probably be able to do it with a simple op-amp. If you get smart there is no reason not to use the digital outputs available on the 6009 to switch conditioning ranges (gain resistors) and you will have all the dynamic range you could ever need!
The trick is in the small words 'correctly configured pre-conditioning amplifier', but it's only a bit of effort.
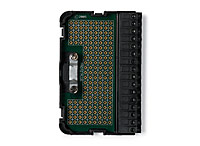
There is a small prototype module available which would allow addition of a conditioning circuit, though measurement stability may be a problem: -
You don't have to use the above prototype module a bit of prototype circuit board will also do nicely as well, its just a few more wires and it will be cheaper.Now with the power supplys available +5v (200mA) and a +2.5v reference available. You need to implement an amplifier which will take the micro volt ouput from the strain gauge and convert it into a value suitable for an input range (probably differential configuration) on the USB device. Without a voltage invertor (like a diode chagre pump type), which invariably add noise, for the op amp you will be limited to a positive only output. The circuit will be a lot simpler though. Alternatively a couple of PP3 9v batterys will probably run for up to a week and give ±9v supply rails. But my intention here is to demonstrate that 'for a few bucks, you can achieve great things'. The exact configuration of this amplifier will depend on the the gauge, the configuration being used for the gauge such as full bridge, quarter or whatever configuration you have decided upon. You should think about an anti-alias filter to remove frequency content outside the range of interest and this will prevent radio interference from aliasing the signal (see note below on screening). I have attached the basis of a suitable circuit which can be used as the basis of the conditioning circuit design.
There is a nice article on strain guage measurement
herePay carefull attention to screening the installation (shielded cables and boxes etc), as the tendancy with strain gauge systems is to pick up every radio signal for a couple of hundred mile radius. Most people end up trying to ignore it by filtering and allowing the noise error to be ignored but with good screening and attention to detail you can get very low noise signals for not much effort.
Message Edité par Conseils le 03-25-200610:43 PM