Hi everyone! My name is Mahtab, and I am the newest addition to the NI Team. I am studying Engineering at the University of Toronto, and have some great experience using Multisim and Ultiboard. Throughout this summer I will be contributing to this blog on a weekly basis. My goal is to use my experience with simulation, circuit design and Multisim, coupled with my unique perspective as a student at the University of Toronto, to write helpful posts on how to be more productive when using our NI tools. I look forward to your feedback and thoughts! 
A few weeks ago, Fernando made a post that dealt with how to create a component based upon a SPICE model downloaded from the manufacturer’s website. But what do you do in the instances when a manufacturer has not (or cannot) provided a SPICE model for their product? Is it still possible to create a custom component?
Fortunately, this is possible in Multisim, and there are a few ways of doing it. One way is to create a SPICE macro model for an IC (a very good tutorial can be found here). Another way, which I will explain today, is to use the Multisim Model Maker, a seldom used tool in the product. Because the SPICE model created by this tool is basic, accuracy cannot be guaranteed. Nevertheless, it is a fast and easy way to create a simple SPICE model.
For this tutorial, I am going to create the TZX2V4A Zener Diode from Vishay (available at http://www.vishay.com/diodes/list/product-85614/). As you can see from the website, the simulation model is not available, but a datasheet is. With the values given on the datasheet, and only these values, we will be able to create our component. In just 8 simple steps (and about 5 minutes of work) we will create a custom diode!
Step 1:
From the toolbar, go to Tools>>Component Wizard. The Multisim Component Wizard will walk you through the steps of creating a component. Fill out Step 1 so it looks similar to Figure 1:
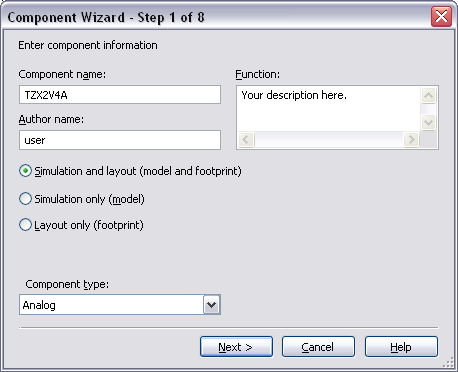
Figure 1 - Component Wizard Step 1
Click Next to go to Step 2, which asks for a footprint.
Step 2:
Click the Select a footprint button and then the Filter button and fill out the fields as shown in Figure 2. Note that you will need to click the Add row button to create each filter.
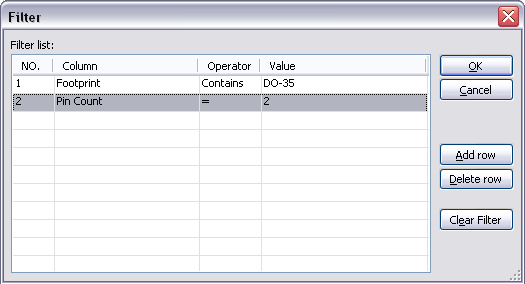
Figure 2 – Component Wizard Footprint Filter
Click Ok to go back to the footprint selection step. It should look similar to Figure 3.
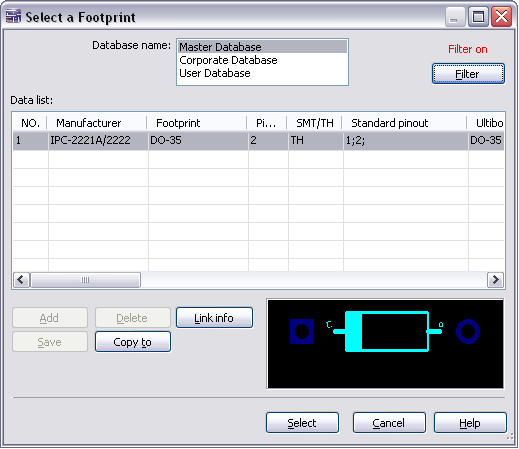
Figure 3 – Select a Footprint
Click Select to confirm the footprint, and you will be brought back to Step 2 of the Component Wizard. In our case, we are working with a Single Section Component, and the Number of pins is 2. Click Next.
Step 3:
Here, we specify a symbol. The default is the rectangle shown, but we are going to change the symbol so it actually looks like a Zener Diode. Click Copy from DB and select any Zener Diode from the Master Database (under the Diode group, Zener family), then click OK (as in Figure 4 below).
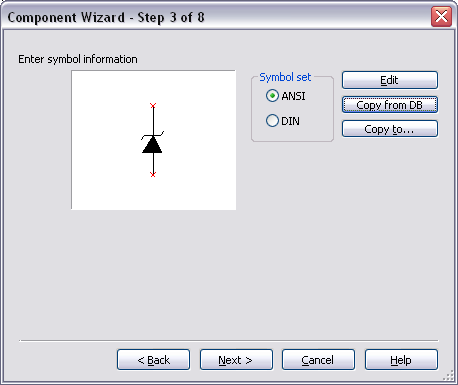
Figure 4 – Symbol Information
Click Next.
Step 4:
Accept the defaults and click Next.
Step 5:
Change the Footprint pins so that the symbol and footprint pins have the same mapping as in Figure 5.
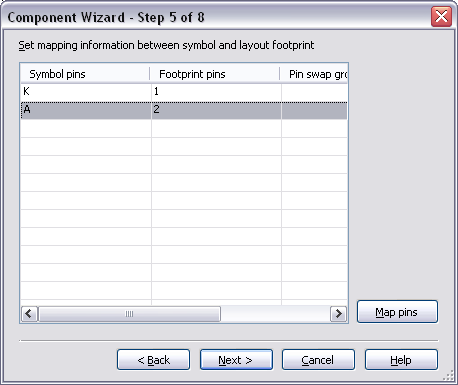
Figure 5 - Mapping information
Click Next.
Step 6:
In this step of the Component Wizard, we are asked for Model Data. If we had a SPICE model we could copy it here; since one is unavailable, however, we can simply use the Model Maker. Click the Model Maker button, and select Zener from the list. Click Accept.
Now, we can use the values from our datasheet to fill in the Electrical Characteristics and the Temperature Coefficient, Capacitance if that data is available. Fill in the appropriate values. In our case, it should look similar to the following image (based upon our datasheet):
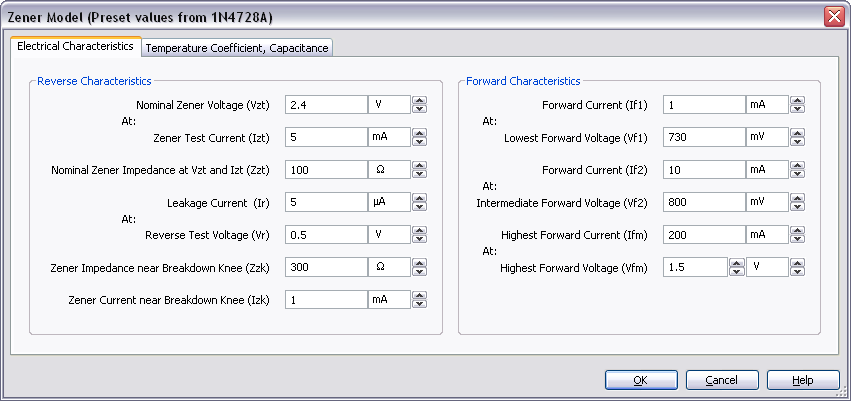
Figure 6 - Zener Model
Click Ok when you have filled in all the data. The values you enter may be different from the above image depending on which component you are creating.
Now we are back to Step 6 of the Component Wizard, and you can see that the Model data has been (magically) filled in. Change the Model name to TZX2V4A and click Next.
Step 7:
Accept the defaults and click Next.
Step 8:
Now we choose a location in the database for our new component. I am going to place it in the User Database, under Diodes. Click the Add Family button and call the family name Zener. Click Ok, select the Zener family you just created, and click Finish.
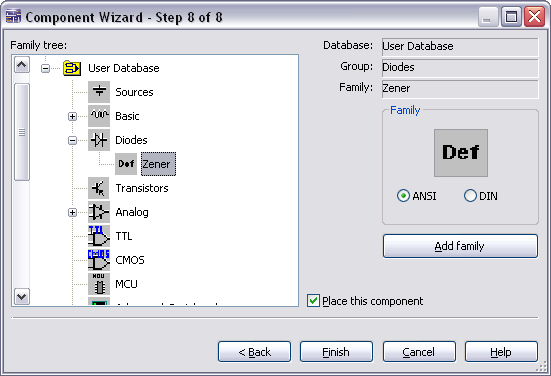
Figure 7 - Component Wizard Step 8
And there you have it – you have created a component using the Multisim Model Maker. You can now test your component by building a test circuit.
Thanks for tuning in!
Mahtab